There is a very famous saying by Aristotle that serves as a very good definition for excellence. He said, “Excellence then, is not an act, but a habit”. Let’s move forward 2400 years to our current days and what Aristotle said in the context of operational excellence still holds true. Achieving operational excellence is indeed a habit. In other words, a continuous and consistent process.
Sooner or later, every company embarks on the journey of operational excellence. It is a difficult complex process that requires a lot of planning, strategizing, and involves making mistakes and learning from them. Whether you already started that journey or you’re about to take the first steps, this article will help you grasp the essence of operational excellence. It will also help you understand its key principles, what to do and which tools to use to achieve operational excellence.
What is operational excellence?
Operational excellence is about optimizing the way a company functions to compete with others in the same industry. It is a philosophy that focuses on continuous improvements by combining current business processes with efficiency methodologies. Lean manufacturing, Six Sigma, and Kaizen are the primary approaches for it. Operational excellence leads to a scalable change on employees, customers, as well as products. It’s not just about improving one process but rather setting the whole organization in an improvement mindset. All employees should contribute by maximizing the efficiency of their workflow and performance.
When we talk about continuous improvement, we refer to cycles of assessing the processes, coming up with cost-effective solutions, looking for opportunities, refining performance, and ensuring everything is executed as best as possible. It is about adopting and making the work habits better. It might take months and even years to reach operational excellence. Consistency is a critical factor.
Operational excellence in practice
Suppose two similar companies were running under the same strategy and processes. The one that implements operational excellence approaches will achieve better results than the other.
For example, companies A and B produced chocolate in their factories and sold it to customers via retail stores. Both used the same strategies, production lines, had similar costs, profit margins, and distribution networks.
When company A decided to go for operational excellence, they engaged production line workers, developed a better shift schedule that allowed for higher performance, and collaborated on solutions to reduce waste in the packaging process. After that, they engaged the drivers, changed the transportation routes, and lowered costs. That resulted in higher profit margins, lower retail prices, and eventually happier stakeholders.
This made company A win the competition against company B because of operational excellence. They didn’t invest more capital, nor did they make significant changes to the product. They only enhanced their operational processes. However, operational excellence is not just about developing the workflow of production lines. It extends way further. Let’s dig deeper into some of its main principles.
The key principles of operational excellence
The underlying foundation of operation excellence is embedded in the Shingo model and the following principles derive directly from it:
- Respect every individual – you can motivate your employees to improve the company by showing them respect and making them feel like essential parts of the business. Keep in mind that appreciation matters.
- Lead with humility – be humble, learn from others, and show your employees that you admire their contributions. Such a culture can guarantee their loyalty and devotion.
- Seek perfection – although you can’t achieve the ultimate model, aiming for it will bring you closer to excellence. Always “Shoot for the stars.”
- Embrace scientific thinking – understanding how everything works leads to better decisions and outcomes. Continuous observation and experimentation of your organization’s processes will keep you on the road to improvement.
- Focus on process – it’s essential to make sure that your processes are performing at their peak. If something goes wrong, don’t blame the people for mistakes. First, check the processes.
More principles to follow
- Assure quality at the source – look for defects from the origins of creation and to the end. When you make sure everything is done correctly, you can reach a level of assured quality.
- Flow and pull value – respond to your customers’ demands and continuously develop your work based on their expectations. Only then can you create an actual value for them.
- Think systemically – make sure the flow of communication is open and consistent between various departments in your company. Think about their performance as a whole interconnected system, not as separated units.
- Create constancy of purpose – clearly communicate the organization’s goals. It gives people purpose and motivates them to perform better.
- Create value for the customer – your customers’ needs should constantly improve your processes and workflows. Evolve your work to match up to their expectations.
How to achieve operational excellence?
Achieving operational excellence differs based on the type of work the company does. Companies that provide services have to implement different methods than manufacturing ones. Each one has its procedures that will dive into the basic levels of structure and start from there.
However, there are general methodologies and tips regarding operational excellence that are adjusted to the specificities of any given industry. Let us briefly go over the three main approaches that we briefly mentioned in the beginning and then go deeper into some specific things you can do.
Lean Manufacturing
Lean manufacturing is about reducing the costs of production without altering the quality of products. Reducing waste and improving the production processes are the key features of lean manufacturing. Waste refers to resources consumed in the production process, but it doesn’t impact the product from the customer’s point of view. In short, it’s about maximizing performance while minimizing waste. For example, transportation costs are a waste because it doesn’t make a difference for the customers. Reducing transportation costs reduces waste, leading to lower product prices and higher profit margins. The lean manufacturing method works mainly with manufacturing industries.
Six Sigma
Six Sigma is a data-driven problem-solving technique. It aims to develop a better customer experience by eliminating defects. It uses the DMAIC approach, which stands for define, measure, analysis, improvement, and control. Six Sigma applies perfectly in managerial and manufacturing systems. Companies that implement Six Sigma do not produce at quality levels below 3.4 defects per million opportunities.
Kaizen
Kaizen is the Japanese word for ‘continuous improvement.’ Applying Kaizen means working together towards the goal of incremental improvements. It involves all the employees in the company. Everyone has to participate. Kaizen is based on the fact that all small changes applied to a company will accumulate over time to produce a significant difference. This method focuses on improving the culture of the company rather than introducing tools to improve the processes.
Many companies have achieved operational excellence, and it helped them survive in the worst circumstances ever. Toyota and General Electric are great examples.
And here are some practical things you can do to pave the way for operational excellence:
Where you are and where you want to go
It is crucial that you begin your journey with a thorough and honest assessment of your company. Therefore you should begin your journey by identifying your strengths and weaknesses, the gaps and challenges. You can do this with the good and old SWOT analysis. As a next step, start to outline your vision and where you want to go. So he clichè “where you want to be in 5 years” question, in this case, is more than appropriate.
Engage everyone in the team
Above all achieving operational excellence is a team effort, so you need all hands on deck. From c-suite to frontline workers, everyone needs to be engaged in the process. Start by explaining to your team what operational excellence entails, why it’s important for the company and what they can do to contribute to it. This can be a bit challenging for hybrid, asynchronous and on-stie teams alike.
The best thing you can do is provide a uniform platform for teams to collaborate. This platform can become your primary communication channel, your announcement board, project management tool and more. Creating such a collective workplace on the virtual realm can take a significant amount of time. However, you can use pre-built templates to avoid building workspaces from scratch.
Structure your business processes
How you manage your resources can make or break your “operational excellence quest.” Streamline your processes by reducing manual work and digitizing whatever is possible. Luckily, you have a myriad of tools available to you to do that. As mentioned above, introducing a collaborative workspace is a great first step. Meanwhile, managing that workspace can become a huge burden as well.
You can reduce or even get rid of that burden entirely by structuring and templatizing the processes that take place within that workspace. Make an effort once, to create a template workspace with all the right people, documents, files, apps and even pre-built tasks, and use that prototype workspace for the rest of your teams/departments.
Monitoring
Effective monitoring depends entirely on proper metrics (or KPIs). Therefore, you need to make sure you have the right metrics since they will show you how much progress (if any) you’ve made in your operational excellence journey. Make sure to make those metrics SMART. These metrics and KPIs vary greatly from industry to industry. You can read more about them here.
Tools to help you achieve operational excellence
In addition to realizing the fundamentals of operational excellence, a tech solution is essential to ensure firm improvements within your organization. Nowadays, many dedicated software provide process analysis, cross-functional flow charts, value stream mapping, and others. Collaboration and project management tools are also essential contributors to operational excellence. It allows fostering the ten principles we mentioned above and the implementation of a suitable methodology.
Data analytics tools
It’s worth investing in a good data-analysis tool that will help you obtain an idea of your past, your present and help you predict the future. The more data-based your decisions are, the more like you are to achieve operational excellence faster and more efficiently.
Templates
Putting all your workflow processes in a template reduces the manual work that must be done repetitively every time within the organization. It also allows for more innovation over the whole workflow. It gives the company an eagle eye from above about how everything is interconnected and working.
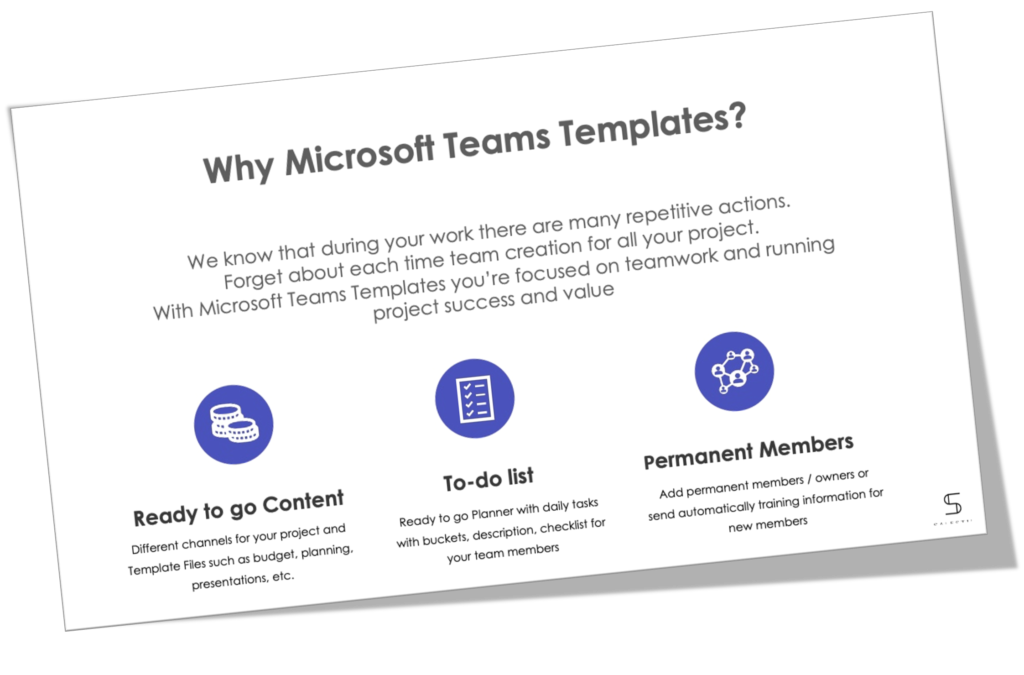
Wondering how to templatize your business processes?
Download our step-by-step guide on how to create Collaboration Templates for Microsoft Teams
Whiteboards and visual collaboration platforms
Operational excellence is strongly linked with understanding your business process. Sometimes the best way to go deeper and to analyze those processes is through creating flows, and various charts and diagrams. That’s where whiteboards and visual collaborative platforms step in. They can be integrated within any collaboration platform like Microsoft Teams.
Join other industry leaders in their journey towards operational excellence, apply the basic principles, choose the perfect methodology that would suit your business niche, and boost your steps with a trusted tech solution that will support you all the way long. In short, always remember that excellence is not an act but a habit.
Templatize your workflows and start leveraging performance today with SalesTim.